Entwicklung und Charakterisierung additiv gefertigter thermoplast-basierter kurz- und endlosfaserverstärker C/C-SiC Verbundkeramiken
Faserverstärkte Verbundkeramiken gewinnen aufgrund hervorragender thermomechanischer Eigenschaften immer mehr an Bedeutung. Im LSI-Verfahren als wichtigster Herstellprozess, wird ein C-faserverstärktes Kunststofflaminat (CFK bzw. Grünkörper) in eine C-faserverstärkte SiC-Keramik (C/C-SiC) umgewandelt. Die Kunststoffmatrix muss aus einem C-Precursor bestehen, der sich in der Pyrolyse zu mind. 50 Gew.-% in amorphen Kohlenstoff umsetzt und abschließend mit schmelzflüssigem Silizium (> 1420 °C) zu SiC reagiert.
Die thermophysikalischen Eigenschaften der C/C-SiC Materialien hängen wesentlich von der Faserorientierung, die Faser- Matrix-Bindung, dem Faservolumengehalt und der Faserlänge ab. Diese Variablen sind für Verbundkeramiken (CMC, Ceramic Matrix Composites) aktuell nur sehr eingeschränkt variierbar. Dies führt dazu, dass es keine Möglichkeit gibt, CMC genau an thermophysikalische Belastungen auszulegen und die Mikrostruktur dementsprechend zu gestalten. Man kann mit Kurzfasern (> 6 mm) endkonturnah arbeiten, aber erhält isotrope Faserorientierungen, nur moderate Festigkeiten und geringe Faservolumina. Hohe Festigkeiten, Faservolumina aber keine Endkonturnähe sind mit C-Geweben zu realisieren.
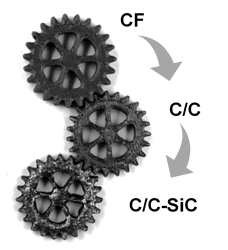
Eine Kombination dieser Vorteile erfordert eine additive, automatisierte, belastungsgerechte Ablage von C-Fasern in der CFK-Fertigung. Dies wird in diesem Projekt angestrebt, um das Anwendungspotential der Verbundkeramiken zu vergrößern. Um mit Kurz- und Endlosfaserverstärkung additiv fertigen zu können wird C-faserverstärktes PEEK im FDM/AFP-Verfahren genutzt. PEEK hinterlässt nach der Pyrolyse mehr als 50 Gew.-% Rest-Kohlenstoff, schmilzt bei > 340 °C aber auf, wodurch sich Grünkörper verformen, delaminieren und aufblähen können.
Es wird daher ein Verfahren entwickelt, um PEEK, thermisch, oxidativ zumindest teilweise zu vernetzen bzw. unschmelzbar zu machen. Dies wird an PEEK ohne Fasern, mit < 0,5 mm langen Einzelfasern sowie Faserbündeln > 25 mm versucht und gelang schon in einigen Vorarbeiten beim Antragssteller. Ist dies erfolgreich, können 3D-Körper, im Gegensatz zum Stand der Technik, ohne formstabilisierende Werkzeuge oder axiale Beschwerungen fabriziert und auch die Mikrostruktur so gestaltet werden, dass die Pyrolysegase durch additive generierte Entgasungskanäle leicht entweichen können. Aufblähungen oder Delaminationen werden dadurch verhindert. Analytisch wird der Vernetzungsprozess des PEEK mittels thermogravimetrischen, kalorimetrischen und rheologischen Verfahren bei Temperaturen bis zu 600 °C untersucht. Dies geschieht, um die Kinetik zu verstehen und parallel laufende Prozesse wie Oxidation, Degradation und Aufschmelzen von der Vernetzung zu trennen sowie um ein Prozessfenster für die Vernetzung zu ermitteln. Zusätzlich wird die Mikrostruktur und die Festigkeit sowie Schadenstoleranz analysiert. Abschließend werden verschiedene Prototypen additiv gefertigt, um das Potential der neuen Fertigungsmethode zu demonstrieren.
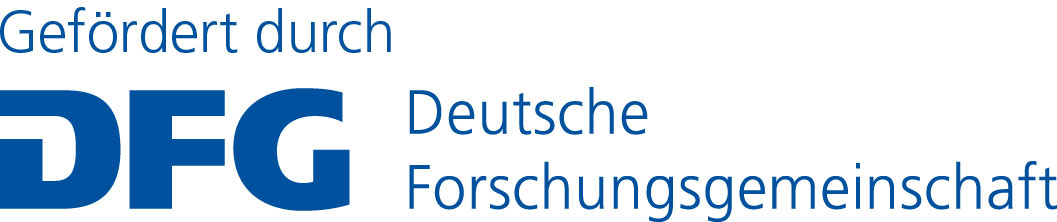
Laufzeit: 06/2021 – 05/2024
Fördergeber: DFG
Ansprechpartner: Dipl.-Ing. Wolfgang Freudenberg, Dr. rer. nat. Nico Langhof